1、 Background of heat shrinkable film
In the beverage industry, there are many brands and varieties, and the market competition is fierce. In order to attract the attention of consumers and gain the favor of consumers, manufacturers, from the perspective of packaging design, have appeared many gorgeous bottle labels, most of which are shrink film labels. At present, shrink film labels have developed into an important part of the label market, and the market share has been expanding, with an annual growth rate of up to 15%, far exceeding the annual growth rate of about 5% for ordinary labels. It has huge development potential and is a highlight of the label printing industry.
With the development of society, the application of shrink film label has been far beyond the outer packaging of beverage bottles, and other industries have gradually found the advantages of shrink film label and gradually increased its application. For example, in the beer industry, in order to facilitate the recycling of beer bottles, the labels attached on the surface are made of heat shrinkable film. When they are recycled, they are immersed in hot water. The labels automatically shrink and fall off, avoiding the use of solvents, greatly reducing the difficulty of label removal, and being more environmentally friendly. The battery industry has also increased the use of shrink film labels, which can effectively simplify production processes and reduce production costs. As well as toys, daily chemical products, household appliances and other industries, the application of heat shrinkable film has gradually begun.
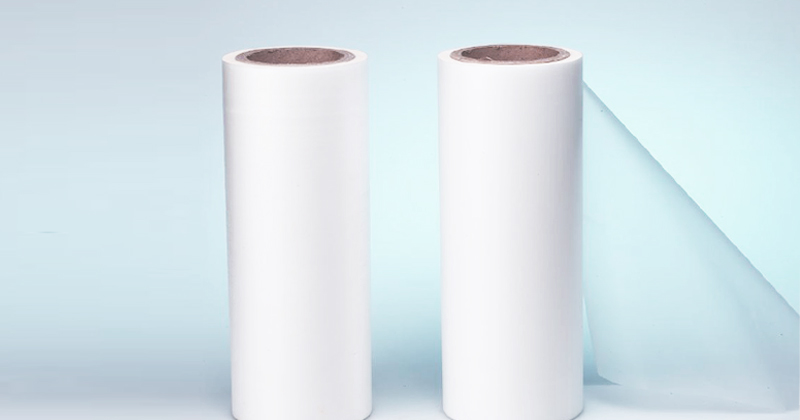
2、 Classification of heat shrinkable films
The heat shrinkable film labels are mainly classified into PVC (polyvinyl chloride), OPS (oriented polystyrene), PETG (modified polyester), etc.
1. PVC heat shrinkable film
PVC heat shrinkable film not only has high production capacity, low cost, large shrinkage (50-65%), but also has a wide temperature shrinkage range. It is the most widely used heat shrinkable label. However, PVC contains toxic plasticizers. Packaging used for direct contact with food is harmful to human health. In addition, hydrogen chloride acid substances are produced during combustion, which may corrode incinerators and may also produce toxic gases, which is not conducive to environmental protection. The use of such shrink films has been prohibited or restricted in some countries and regions.
2. OPS heat shrinkable film
OPS heat shrinkable film has small shrinkage force, good shrinkage uniformity, and the shrinkage rate is close to 70%. It is widely used in Japan, where OPS has completely replaced PVC in the field of heat shrinkable film. However, the Tg point of OPS is low, and deformation will occur at about 40 ℃. The shrinkage of OPS is large when it is stored at room temperature, so it must be stored in cold storage. Its application is limited. It is only widely used in Japan, a mature country or region for production, use, and post-treatment.
3. PETG heat shrinkable film
As a kind of label film, PETG heat shrinkable film has a high shrinkage rate (60-80%), which can be applied to many bottles with complex geometric shapes for large-area labeling. Moreover, the shrinkage curve of PETG is relatively flat, which is convenient for more accurate control of the thermal shrinkage of labels. However, the production process of PETG is relatively complex, and one of its raw materials, CHDM (1,4-cyclohexanedimethanol), is expensive, resulting in the price of PETG being much higher than PVC.
3、 Development of PETG heat shrinkable film
As a heat shrinkable film for labels, it needs to have good shrinkage, wear resistance, weather resistance and printing performance. Compared with other materials, PETG heat shrinkable film has the characteristics of high ultimate shrinkage, low natural shrinkage, flat shrinkage curve, high transparency and glossiness, and excellent printing color. And PETG and plastic bottle body belong to polyester series, which has unique advantages in recycling, and is internationally recognized as environment-friendly heat shrinkable packaging materials.
1. PETG History
PETG is a terpolymer composed of PTA (terephthalic acid), EG (ethylene glycol) and CHDM. There are mainly two synthesis methods: direct esterification (PTA) and transesterification (DMT). Eastman of the United States took the lead in mastering the core technology, successfully developed and put into the market. Subsequently, SK Company in South Korea developed PETG with PTA method, which was officially put into production in 2001. The research on PETG started late in China, and since the main patented technology of PETG is in the hands of Eastman and SK, domestic PETG mainly uses NPG (neopentyl glycol) or a variety of diols to polymerize instead of CHDM, reducing the crystallization performance of PET, and obtaining low crystalline or amorphous PETG copolyesters, among which Shanghai Petrochemical and Guangdong Tree Industry have been able to stably produce PETG chips and form sales.
2. Development of PETG heat shrinkable film
Although the main core technology of PETG has not been broken through in China for the time being, the production and application of PETG film has been greatly developed in China. The production method of PETG film is mainly unidirectional stretching, and the production equipment is Bruckner, Germany, Japan Steel Institute or some domestic equipment. Due to the small market demand for PETG, several companies in China, such as Guangdong Huaye and Henan Yinjinda, have special production lines for PETG, and most of the rest are PET film manufacturers who adjust their production processes on their own production lines as differentiated products, such as Jiangsu Eskexi, Suzhou Kepei, Shandong Fuwei and Yixing Guanghui. Later, Jiangsu Shuangxing set foot in the field of PETG film, The price of PETG heat shrinkable film was reduced to below 18000 yuan/t (about 14000 yuan/t to 16000 yuan/t) for the first time, and the price limit of PETG in market application was further reduced.
The thickness of PETG heat shrinkable film is mainly 45~50 at the beginning of its birth μ m. With this thickness, the stiffness of the film is better, the printing and labeling of subsequent processing will be easier, and the aesthetics of the label will be better. With the maturity of production and processing technology, the thickness of PETG film gradually decreases, but the stiffness and other mechanical properties of the film also decline. To ensure the production efficiency of the high-speed labeling machine, the thickness of most products at present is 36~45 μ m。
3. Application of PETG heat shrinkable film
At present, European and American countries have not explicitly prohibited the application of PVC in the field of heat shrinkable film, but many large international enterprises represented by Coca Cola have taken the lead in their environmental awareness and have replaced the outer packaging shrink film of products from PVC to PETG in advance. As early as 2010, Coca Cola Company has started to transform its labels such as "Guoli Orange" and "Guoli Milk Yo" from PVC to PETG, and international large beverage enterprises such as Pepsi Cola and Nestle have also changed many of their shrink labels to PETG film. In terms of daily-use chemicals, Procter&Gamble, Unilever, etc. overcame a number of technical difficulties and changed the heat shrinkable labels of their "Xiashilian", "Lishi" and other brands to PETG. Many domestic beverage enterprises are also gradually strengthening their investment in environmental protection. For example, many products of Wahaha, Nongfu Shanquan and other enterprises have been packaged with PETG, and the battery outsourcing label of Nanfu, the leading battery enterprise, is also PETG. With the maturity of PETG heat shrinkable film process and the further reduction of cost, the application scope will be further expanded to replace other heat shrinkable films, especially PVC.
4、 Production and technology of PETG heat shrinkable film
1. Raw materials
In essence, PETG is a modified PET polyester, so the production of PETG film is similar to PET. According to the functions of the main/auxiliary extruder, the raw materials are divided into bright chips used in the core layer and functional masterbatches used in the surface layer.
2. PETG film production process
As a modified polyester film, the performance and downstream application of PETG shrink film are greatly different from ordinary polyester, and the production process is also different from ordinary PET.
2.1 Drying
PETG modified by NPG is easy to be degraded by water during processing in China. For some companies using single screw extruder, PETG needs to be dried in advance before entering the extruder. PETG that still has a certain crystallizing capacity is usually dried in a rotary drum at 110 ℃ for more than 4 hours, while amorphous PETG is dried in a drying tower at low temperature (below 70 ℃) for 4 to 6 hours. If the extruder is twin-screw type, the vacuum exhaust system provided by the extruder can effectively remove the moisture in PETG, so the drying step can be omitted.
2.2 Extrusion
The performance difference between PETG and PET is shown in the following table. The melting temperature of PETG is low, and the processing temperature is generally 240-260 ℃. The processing temperature of twin-screw extruder can be further appropriately reduced due to more severe shearing. It is worth noting that due to the amorphous nature of PETG, it is easy to stick and agglomerate under high temperature conditions. If the temperature at the inlet of the extruder is too high, it is easy to bridge the blanking port. Therefore, the inlet temperature of the extruder is usually reduced to below 200 ℃ during production.
2.3 Stretching
PETG film is a shrink film. According to the requirements of downstream applications, it is generally unidirectional shrink, namely MD stretch and TD stretch. MD stretch is mainly used for battery labels, with low market demand and few manufacturers. Most PETG films in China are TD stretched. Because the beverage labels are generally shrink labels by the nested labeling method, PETG shrink films are required to shrink laterally along the bottle body. Some shrink films with higher requirements will be designed with a slight stretch in the MD direction during production (the stretching ratio is less than 110%) to prevent the longitudinal size of shrink labels from naturally increasing when they shrink laterally in subsequent applications.
TD drawing process generally has two design ideas: ① higher preheating temperature and lower drawing temperature; ② The preheating tensile temperature is designed by the progressive method similar to BOPET. Both ideas have advantages and disadvantages, mainly depending on the production line.
Shrink film generally needs to be shaped at 60-70 ℃ to release internal stress. If it is a material with certain crystallinity, it also needs to be cooled quickly to prevent crystallization during product cooling, which will affect the shrinkage, optical and mechanical properties of the product.
As most printing plants use solvent based ink for printing, PETG shrink film generally does not need corona treatment. Without corona treatment, the static electricity on the product surface can be well controlled to prevent the subsequent processing and use from being affected by excessive static electricity.
2.4 Rolling, slitting and packaging
PETG film should be used as a label, and the subsequent multi-step processing process is required. During the winding, good tightness and apparent flatness should be ensured to avoid problems such as inaccurate color registration during subsequent printing.
2.5 Storage and Transportation
PETG is amorphous, and its softening point is low (about 70 ℃). PETG film may deform under high temperature environment for a long time, resulting in size and appearance deterioration, which will also affect subsequent printing and other processes. Therefore, PETG film shall be stored in a dark and cool place, and long time sun exposure shall be avoided during transportation.
5、 Processing and Application of PETG Heat shrinkable Label
Changing PETG heat shrinkable film into packaging labels for beverages on supermarket shelves requires multi-step follow-up processing steps such as printing, slitting, palm folding, and labeling. The representative shrink label manufacturers in China mainly include Beijing Amco, Shanghai Ziquan, Hefei Siai, and Zhejiang Chengxin. Among them, Beijing Amco is the world's largest label manufacturer and one of Coca Cola's shrink label suppliers. As the second largest label manufacturer in the world, Hefei Siai is the largest manufacturer of beer labels. It has established long-term cooperation with Heineken, Tiger and other beer enterprises that use shrink labels.
1. Printing
Heat shrinkable film labels have many colors, complex patterns and large printing volume. In order to ensure the printing quality, most of them use solvent based ink for intaglio printing to ensure the hierarchical and three-dimensional design. With the improvement of environmental protection requirements, some enterprises are gradually beginning to use water-based ink and flexographic printing. Due to the shrinkage characteristics of PETG, the printing ink can only be dried by cold air after printing, and the requirements for printing ink are high.
2. Slicing
Generally, the printing factory will select 3-5 layouts to print at the same time according to the width of their respective printing presses and product width, and then use the slitter to cut into small rolls of a single layout after printing.
3. Palm joint
PETG labels usually use the labeling process. Before entering the labeling workshop, the labels need to be made into a cylinder. The mixed solution prepared by a variety of solvents is applied to the printed palm line as a micro coating of palm glue. The glue slightly corrodes PETG to make it sticky, and then it is laminated, compacted, made into a cylinder and rolled for storage. There are also some manufacturers who manually set labels and cut them into single labels after palming.
4. Set of standards
Generally, the final product is made by combining the labeling machine with the steam shrinking furnace, and a small part of the finished product enters the steam shrinking furnace after manual labeling.
- Share
-
12
- PETG plastic bottle - the next trend of skin care packaging materials
- 正在更新中...